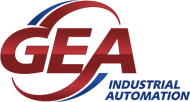
When planning for industrial control panels, designers usually look first at ways to save on product costs. While initial cost savings may be important, it’s reliable and trouble free operation that will save money in the long run.
Moreover, companies often overlook the importance of their industrial control panels and tend to focus more on the mechanical systems and operating equipment powered by them. Every facility should pay close attention to the proposed location of the panels as well as the environmental conditions in which they will be placed.
Not only is the electrical equipment housed inside the control panel a significant component of the overall facility cost, it also is a vital component to the business’ operations. Careful planning should include these five often overlooked cooling considerations to help ensure high efficiency and trouble-free operation.
1. The Effects of Heat Load and Ambient Temperatures
One of the largest killers of electrical equipment is excessive heat. Component manufacturers specify a maximum operating temperature for their products, but to ensure the longest life possible it’s best to maintain operating temperature around 95°F (35°C). Since all electrical components produce heat, they will most likely require cooling from filtered fans, air-to-air heat exchangers or enclosure air conditioners.
An often overlooked part of industrial control panel design is a realistic view of ambient temperature extremes. Temperature fluctuations, seasonal weather changes or even a location in close proximity to heat producing equipment can adversely affect electrical components causing overheating and failure.
2. Required Cooling Capacity
In order to provide adequate cooling, the required cooling capacity must be established. The importance of assessing the total heat load is often overlooked.
By using an enclosure temperature management (ETM) calculator, it is possible to source a cooling solution with sufficient capacity to properly cool the enclosure. Failing to overlook this important step can result in the purchase of an improperly sized cooling system. An undersized cooling system will be overworked and an oversized system could fail to maintain a consistent desired enclosure temperature.
3. Considerations for Difficult Environments
Cooling systems required to operate in dusty and corrosive environments will require a regular scheduled maintenance program. Air filters may need frequent cleaning or replacement, condenser coils and fan blades will need inspection for dust accumulation.
Ignoring maintenance can lead to blocked filters and condenser coils causing not only electrical component failure but also damage to the cooling systems resulting in voided warranties.
4. Solar Heat Gain
In addition to knowing the maximum ambient temperature surrounding the industrial control panel, the effects of solar heat gain in outdoor installations must also be considered before choosing a thermal management system.
The effects of solar radiation on control panels can cause the internal temperature to rise dramatically. Choosing an industrial control panel with a reflective color or utilizing shielding should be considered to decrease solar heat gain. Using the enclosure temperature management calculator will help account for solar heat gain.
5. Choosing the Correct Industrial Control Panel Size and Type
NEMA ratings are designed to help protect electrical components, personnel and property from damage. Environments involving high pressure water, abrasive cleaners and corrosive materials require the use of specific NEMA rated control panels. Understanding NEMA standards can help simplify the process of choosing the correct industrial control panel.
The importance of determining the correct industrial control panel size shouldn’t be overlooked. An undersized control panel will not allow for future expansion and proper cooling due to restricted air flow. An oversized industrial control panel may require a larger, more expensive, thermal management system, increasing the overall cost of the installation.
Planning ahead for proper industrial control panel cooling
Proper planning will help alleviate potential thermal issues. Industrial control panels should be located in an area with adequate ventilation, away from dust and corrosive materials and away from direct sunlight if possible. Keeping these important cooling considerations in mind will help ensure a long reliable life for your electrical equipment, keeping costs lower in the long run.
Before choosing a thermal management system for your Industrial control panel, contact the experts at Thermal Edge to find the best possible cooling solution for your application.